I had a good time researching glass for my previous material science post, and it got me thinking about other materials we often take for granted. Another source of inspiration for this post was the observation in The Human Advantage that the invention of new materials has been roughly exponential beginning from the advent of agriculture. The author provides a list of “the first ninety that come to mind”:
stone, fire, obsidian, wood, bone, ceramics, copper, plaster, bronze, asphalt, cotton fabric, silk, gold, silver, graphite, glass, terracotta, parchment, papyrus, iron, latex rubber, wool, ivory, steel, pewter, marble, concrete, alum salts, paper, blown glass, naphtha, coke (fuel), petroleum oil, porcelain, gunpowder, dental amalgam, glass lenses, mirrors, molten glass, Portland cement...
And I was surprised by how many I didn’t recognize, and how many others I realized I didn’t fully understand. In this post, I’ll go over a few of the major families of materials I found more interesting: how they’re made, what they’re made of, how they work, and how they’re used.
Ceramics
Ceramics have been used for at least the past twenty-six thousand years and have been continuously improved upon since then. Clay, or rock containing minerals composed of aluminum, silicon, and water, is naturally occurring and very common, and can be shaped by hand and then air-dried into a solid, something any caveman with access to clay would quickly discover. The next step, putting it in a fire, is what turns it into ceramic, and also seems quite easy to discover–what kids don’t naturally put everything they can think of into a campfire to see what happens?
Clay gets its properties from its microstructure. It is made up of microscopic water-containing crystalline plates with additional water in between them, which allows the plates to cohere through hydrogen bonding but also slide past one another. Air drying removes the water between the plates but leaves the water in the crystals intact, resulting in a green part, which can be rehydrated to form workable clay again. Firing at high temperatures removes the water inside the crystals, forcing the clay to recrystallize into a different, insoluble mineral known as metakaolinite. While adding water to fired clay won’t make it moldable again, the ceramic is porous and will absorb water into its microscopic cavities that isn’t easily removed. Bacteria can then breed in the water-filled stagnant cavities and release toxins, which renders the piece not food-safe. To mitigate that, potters add glaze, which melts in the kiln and adheres to the clay, producing a nonporous, glassy outer surface.
Ceramics are generally divided based on the temperature at which they are fired, with higher temperatures resulting in stronger and less porous products. The lowest and most ancient grade is called earthenware, of which bricks are a very common example. Terracotta is another type of earthenware that has a high iron content, which oxidizes when firing to produce its characteristic rusty red color. Firing hotter results in stoneware, which is still sort of earth-colored, but some of its mineral components have vitrified during firing, or become uncrystallized and flowed like molten glass to fill pores. Vitrification isn’t the same as melting, when something becomes liquid when the temperature is increased; it refers to a range of temperatures over which the material gets more and more liquidy while still remaining semi-solid. Due to this, stoneware is more water-resistant than earthenware but still requires glaze to be considered food-grade.
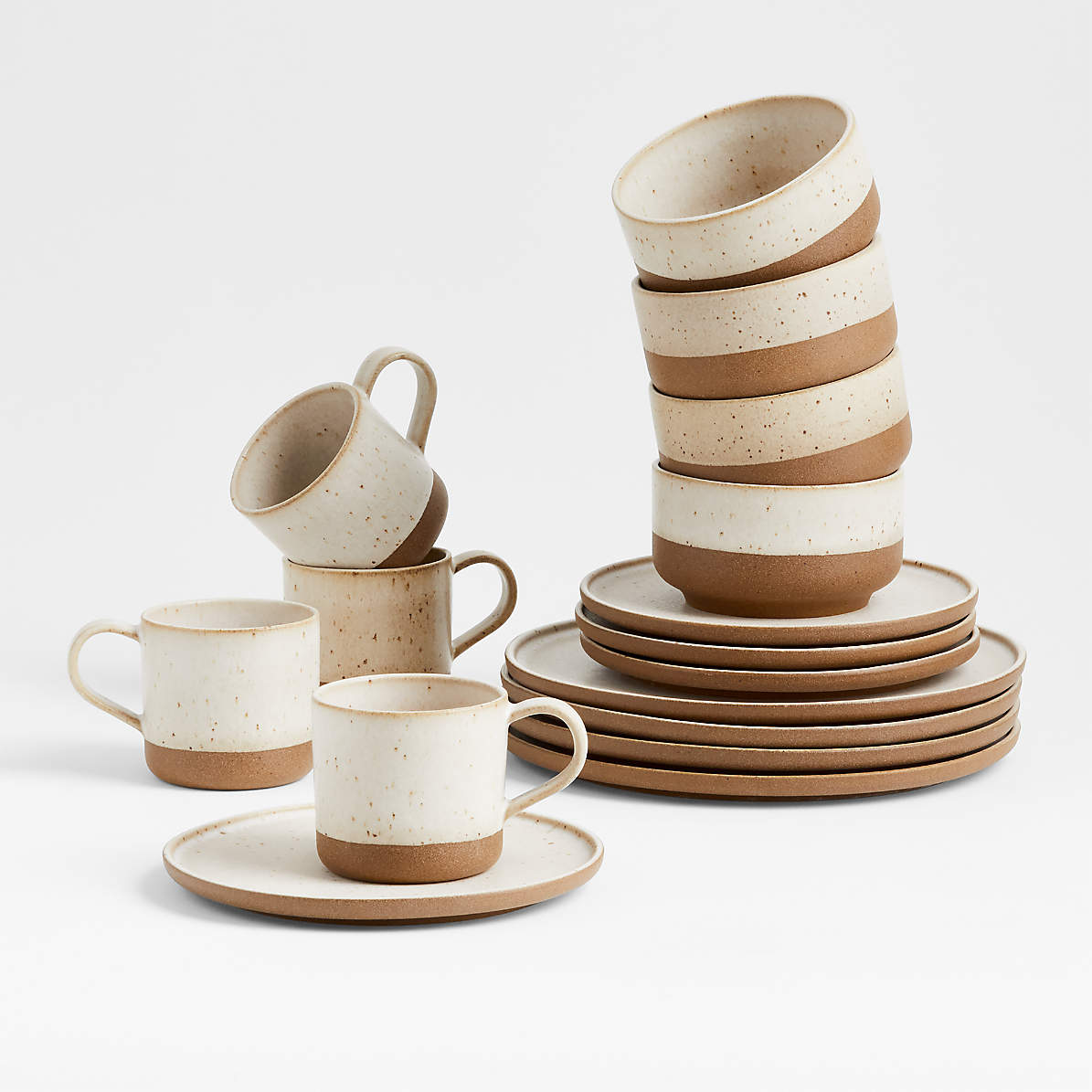
The most common clay mineral is called kaolin. Shale is made mostly of kaolin deposited in layers and compressed, and slate is shale that’s been exposed to heat and pressure. In that sense, shale is similar to earthenware and slate to stoneware, but they differ in a couple of important ways. First, shale contains other minerals in addition to kaolin that don’t make good pottery clay. And second, shale and slate are highly anisotropic, or having different properties depending on the direction in question. Since shale is deposited one thin layer at a time, and then during its metamorphosis into slate it’s pushed and twisted in particular ways, they tend to cleave along certain preferential lines, while clay is more isotropic, with the same strength in all directions.
Fire tends to only reach temperatures of 600 to 1100 degrees C, which is the range defined as producing earthenware. To achieve hotter temperatures, a kiln is required–an insulated space that can keep the heat from escaping. Stoneware is fired between 1100 and 1300 degrees C, and firing clay above 1300 C produces porcelain. Kilns capable of producing porcelain were developed around 200 AD in Asia. At that high of a temperature, the crystal structure of metakaolinite rearranges itself again into mullite, which is stronger, paler, and translucent. Furthermore, the vitrifiable components are fully vitrified, so the end result is nonporous and doesn’t need glaze.
Note: You may have heard the term “vitrification” in reference to cryonics. It does refer to the same phenomenon–a flowing, noncrystalline, glass-like solid–but approaching that state from the opposite direction, from freezing liquid instead of melting solid. If you freeze a living tissue, such as a bag of peas, in a normal freezer, ice crystals grow inside the pea cells and their sharp edges puncture the cell walls. This isn’t a big deal for a food (although too much of this effect is detectable as freezer-burn), but it’s a big problem if you expect the thawed tissue to stay alive, such as an egg cell or a whole human. Therefore, through a few different methods, cryonicists attempt to induce vitrification of ice within the cells–it’s still ice, but a flowy, not-sharp, non-damaging version.
In the late 18th century, Josiah Spode of England, who you may have heard of, invented bone china, a variant of porcelain that contains up to 50% purified ash from usually cow bones. The inclusion of hydroxyapatite from bone changes the resulting crystal structure, increasing the ceramic’s mechanical strength.
Plaster
Plaster is the stuff your walls are made of. But what is it? It seems too flimsy to be stone, as you can punch a hole in a wall if you try hard (though it’s not recommended). But it doesn’t seem similar to any other familiar materials either, other than maybe clay.
Plaster of Paris
It turns out that it actually is stone, specifically gypsum, a mineral that’s so soft you can scratch it with your fingernail. (Gypsum is the reference mineral defining the value 2 on the Mohs hardness scale.) Gypsum can be cheaply shaped into nice flat walls because, like clay, it incorporates water into its crystal structure. This means if you bake it at a temperature high enough to drive out the water, you’re left with powder that can be rehydrated later to turn it back into a rock. This is known as plaster of Paris, because it was first made using gypsum mined in Paris.
Plaster of Paris is used in making casts to keep broken bones straight, although less commonly now that pre-fabricated fiberglass casts are available. One has to be careful not to burn the patient, as the setting reaction is exothermic, meaning heat is released as the plaster powder plus water mixture crystallizes. In one famous case, a schoolgirl stuck her hands into a bucket of wet plaster of Paris in art class and sustained severe burns, as she couldn’t remove her hands as it set.
People used to build houses using a method called “lath-and-plaster”, in which builders would nail wood slats (laths) between studs and then coat plaster over it. Nowadays, they use pre-fabricated sheets of drywall instead, as hanging those is much less time-consuming. But drywall is still made of plaster–it’s extruded and strengthened with paper or cloth.
Alabaster is a form of gypsum that’s particularly pale, translucent, and fine-grained. It has been used for centuries as a medium for carving statues, since it’s pretty and its softness makes it easy to cut with a knife. However, alabaster statues can’t be used outdoors, since they would be damaged by rainfall over time. This is also what “water damage” is in homes. If drywall is exposed to moisture, the gypsum can absorb it, causing swelling and softening.
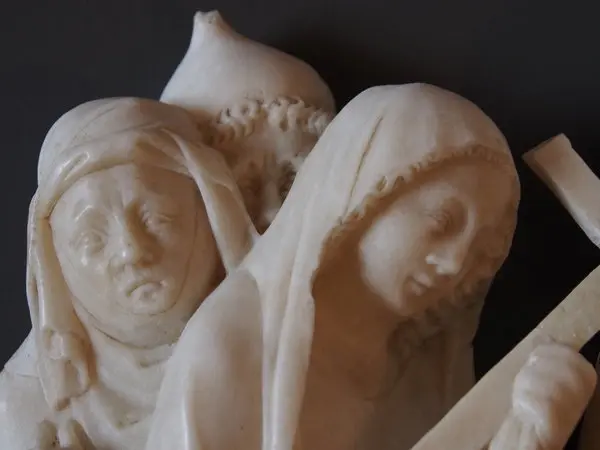
When I was a kid, I sang “America The Beautiful” in choir and wondered at the meaning of the line, “thine alabaster cities gleam”. (If this doesn’t ring a bell, it’s because it’s in the second verse, which no one knows.) Turns out cities are actually made in large part of alabaster!
Lime plaster
There are a couple other types of plaster that aren’t made of gypsum. Lime plaster isn’t as commonly used as gypsum plaster, but has some advantages. It works on the same principle of dehydrating and rehydrating a rock, but with limestone instead of alabaster. The dehydrated powder that results when limestone is baked at high temperatures is called quicklime, which when mixed with water is caustic and requires special care to avoid chemical burns. Once it sets back into limestone, it’s no longer dangerous to touch (though its slight remaining causticity helps to prevent mold growth), and is more flexible and rugged than plaster of Paris.
While it can look similar to cement when applied carelessly, there are a few artistic techniques unique to lime plaster that keep it in use. Venetian plaster refers to a method of applying very thin layers of lime plaster with additives to change the texture and color, and then polishing it, resulting in a surface that looks similar to marble.
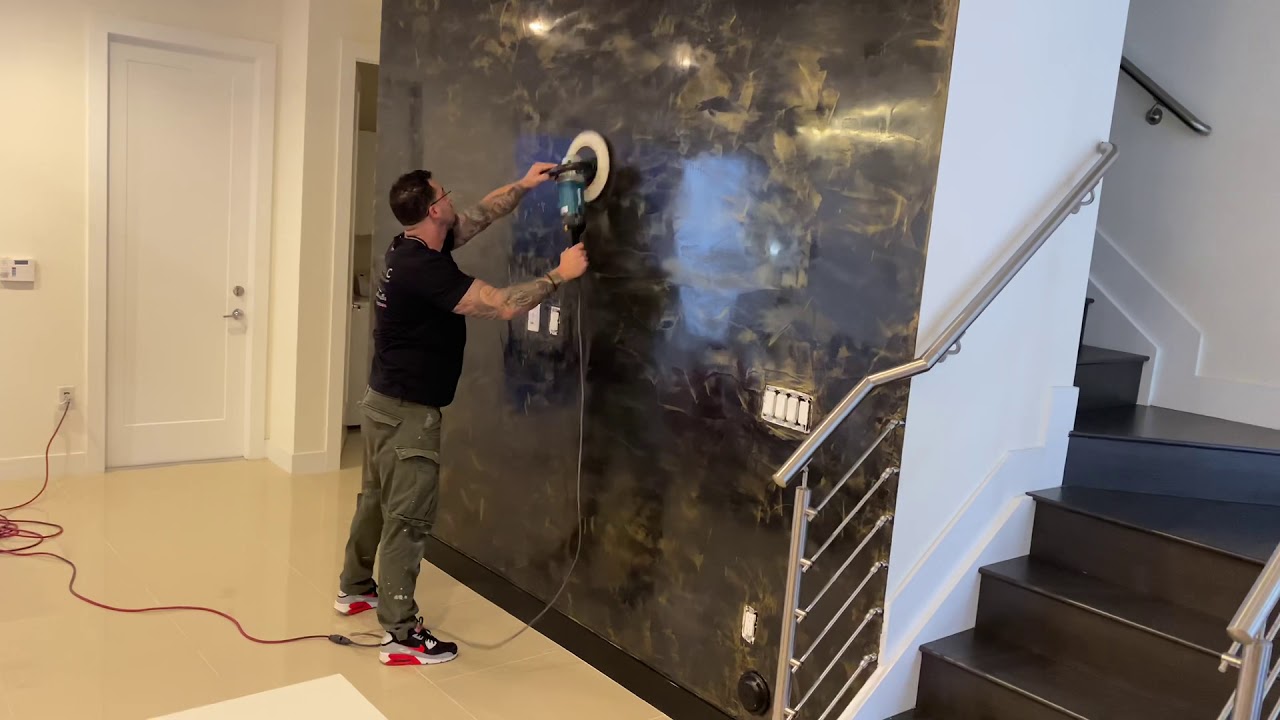
Lime plaster is also used in fresco, the painting technique used by Michelangelo on the ceiling of the Sistine Chapel. Fresco (meaning “fresh”, referring to the wet plaster that needed to be freshly applied just before painting) requires lime plaster specifically for a couple of reasons. First, lime plaster takes longer to set–twelve hours for the thin layer normally used in fresco, giving the artist time to work. Second, relative to limestone, quicklime is short one carbon dioxide molecule, which burns off in addition to the water when it is baked. This means that as lime plaster sets, it absorbs carbon dioxide from the air, changing its chemical formula and making it insoluble to water. This reaction causes a big molecular shuffle that lets the paint become incorporated into the crystal lattice, which doesn’t happen with gypsum plaster. This results in murals that are integral with the wall, which makes them very durable. Whitewash is also a form of lime plaster that’s thinner and more watery, and doesn’t include additives like sand for strength.
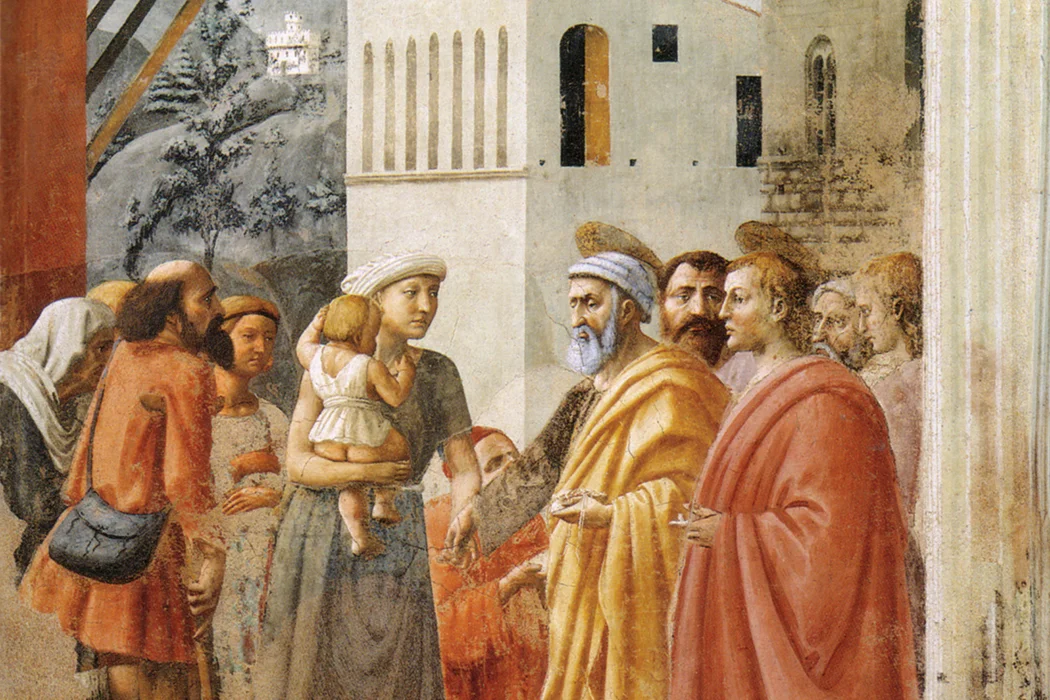
Clay “plaster”
In ancient times, clay was used to line walls (which were also often made of clay) in a similar fashion to plaster. As I covered above in the “ceramics” section, clay air-drying doesn’t work in the same way as plaster setting, and without firing at high temperatures (which would be challenging to do for an entire building), clay is able to be re-hydrated. Therefore, adobe buildings aren’t waterproof, which is why they occur primarily in dry climates. Clay buildings are also brittle and not very strong, so they’re easily damaged by earthquakes. However, one advantage of clay as a building material is that clay has a very high specific heat and an ability to absorb a lot of moisture from the air. This buffers the temperature and humidity inside of clay buildings, allowing them to stay at a moderate temperature while the outside temperature fluctuates.
Portland cement and concrete
One last substance that’s uncommonly used like plaster but very commonly used as a building material is Portland cement, which is basically all the powers of the other plasters combined. To make Portland cement (so called because it looks similar to stone from the Isle of Portland in England), you heat limestone and clay, grind up the resulting nodules (known as “clinker”), and then add gypsum. It was patented in 1824 and is the principle ingredient in concrete, which is the second-most-consumed substance in the world after water. Portland cement is also commonly used as mortar, grout, and stucco (which refers to any decorative plaster-like substance that sticks out from walls, cement or not, interior or exterior). Because Portland cement contains both lime and gypsum, the setting reaction is both caustic and exothermic. Breathing cement dust can cause internal chemical burns as the dry cement is hydrated by water in the lungs.
As I said in my post about glass,
Rebar-reinforced concrete is a common example of a composite material. Rebar (long steel cables) is really strong against tension, but provides basically no resistance when compressed, instead just buckling. (Imagine pulling on a string versus pushing on it.) Concrete is really strong in compression, but useless in tension–it just cracks. When combined, they make a material that’s strong against all kinds of loads. Note: rebar-reinforced concrete is stronger, but the difference in thermal expansion behavior between them, and the fact that rebar rusts over time, means that rebar-reinforced concrete doesn’t last centuries. Roman concrete structures are still standing more than a thousand years later because they were engineered in such a way that they didn’t require metal reinforcement.
I’ve since learned the reason rebar corrodes over time even when embedded in concrete. As long as concrete is alkaline, it inhibits corrosion reactions from occurring. However, over long periods of time carbon dioxide from the air permates in, deep into the solid concrete, and acidifies the environment, accelerating corrosion.
Concrete has pockets of empty space to varying degrees, from nanoconcrete’s less than 0.5mm gaps, for high strength, to pervious concrete’s 15-20%, for water filtration. There’s so much we can do with concrete nowadays; if you major in civil engineering, you can generally expect to take at least three semesters of concrete class. You have to really love concrete!
Technically, the term “concrete” refers to any composite material made of a binding agent and solid particles (“aggregate”). The word comes from the Latin con, meaning “together”, and crescere, meaning “to grow” (the same root as crescendo). The concrete that is normally used in building construction uses Portland cement as the binding agent, and any number of things as the aggregate, including gravel, crushed recycled concrete, sand, and slag (waste material from metal processing). Before Portland cement was invented, quicklime or asphalt were used as the binding agent for concrete, and asphalt concrete, known as blacktop, tarmac, macadam, or simply asphalt, is what we still use to pave roads. Which brings us to…
Asphalt, tar, and other hydrocarbons
Hydrocarbons are a family of compounds made up primarily of hydrogen and carbon in chains, sometimes looped around into rings. There are thousands of modern applications of hydrocarbons, such as plastics, fuels, fertilizer, cosmetics, pharmaceuticals, pesticides, refrigerants, solvents, and many others, but I won’t go into those. Instead, we’ll look only at the ones available to ancient humans.
Now for the real video game crafting. Many useful hydrocarbons come from burning stuff in an environment low in oxygen, like an underground kiln: burning pine wood in an anoxic environment separates it into wood tar, turpentine, and charcoal, while burning coal or petroleum in anoxic conditions makes coke and coal tar. After that, liquid products can be distilled to further separate their components, often by heating it to a particular temperature at which some components will boil and others won’t. Distilling wood tar or coal tar produces creosote, naphtha, and pitch. Burning petroleum (crude oil) in anoxic conditions produces asphalt, coke, tar, and a bunch of other stuff like gasoline.
As I said in a previous post, fossil fuels come from ancient plants and algae, with coal coming from Carboniferous Lepidodendron trees that were buried in anoxic bogs and therefore didn’t decompose the normal way, and petroleum and natural gas coming from algae that sank to the bottom of lakes and oceans, which also tend to be anoxic. New petroleum and natural gas are still being created as modern algae die and sink to the bottom, but at a much lower rate than they’re consumed, which is why they’re considered non-renewable.
Asphalt
Generally, tars are thinner liquids than pitches, of which asphalt is one type. In addition to being a byproduct of petroleum processing, asphalt, also known as bitumen, is naturally occurring, and is what is actually bubbling up at the so-called La Brea Tar Pits, rather than tar. If you haven’t been to the La Brea Tar Pits, I recommend it. The sheer number of fossils in such a small area is staggering, and it’s all big, charismatic Ice Age animals like woolly mammoths and saber-toothed cats. They have about a hundred dire wolf skulls mounted on the wall! What causes all these animals to pile up isn’t that they sink like quicksand, but that their feet get glued in place by the sticky asphalt. There they struggle and make a lot of noise, which attracts predators, which also get mired. So, unlike the environment in which prey outnumber predators by over thirty to one, at a predator trap like La Brea the predators outnumber prey seven to one.
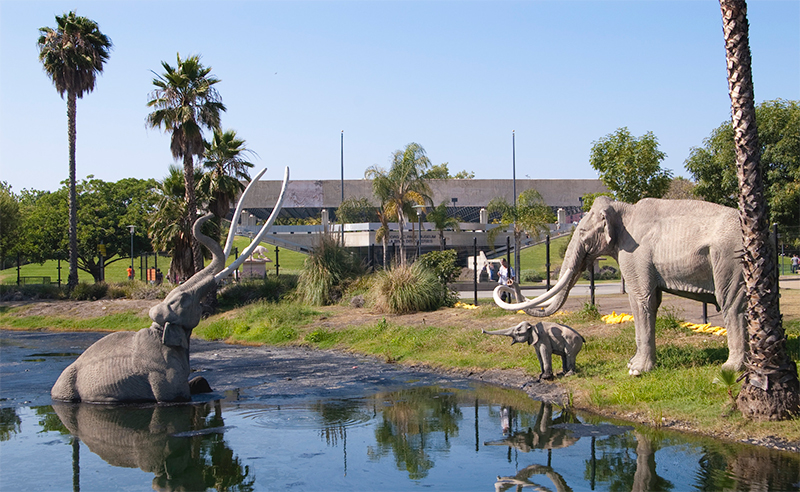
Pre-contact people in the area used the asphalt from the pits to waterproof boats and roofs. There is only one human fossil known from La Brea, dated to between 10,260 and 10,230 years old. She was between 18 and 25 when she died and was only 4’8” to 4’10” tall (it’s only a partial skeleton). While this skeleton is housed at the museum at La Brea, it’s not on display for dumb political reasons.
Tar
In areas where asphalt wasn’t readily available, wood tar was used for many similar purposes: waterproofing ships, roofs, and wooden exterior walls. Unlike asphalt though, tar was sometimes used as a medicine or even candy, especially in northern Europe. In fact, you can still buy tar-containing Finnish liquorice on Amazon. It apparently tastes smoky and sweet. Would you try it?
Pine tar is also used in baseball to improve a hitter’s grip on the bat handle. The rules state that the tar can’t extend past the bat’s logo or else it risks affecting how the ball moves; a famous violation of this occurred in 1983 when Royals player George Brett’s home run was voided and he threw a toddler-worthy tantrum. (The call was overturned 25 days later and they played the rest of the game, ending in a Royals victory.) Pitchers also used to secretly put it on the underside of their hat brims, and then touch their fingers to it just before a pitch to increase the amount they could spin the ball. This usage is illegal, but would only be investigated if the opposing team’s manager made a request, which was seen as unsportsmanlike, allowing the practice to continue. In 2010, an even stickier substance was invented called Spider Tack, intended to be applied to strongmen’s arms and bellies when lifting big round Atlas stones. Pitchers started using this instead of pine tar, and finally in 2021 a new league-wide rule was implemented calling for regular inspections of the pitchers for grip enhancing substances regardless of whether anyone asked for it, which in theory ended the practice.
Thousands of years ago in Europe, Neanderthals and ancient humans chewed on pieces of semi-solid wood tar. Tar has anti-microbial properties, so it may have been used like chewing gum to clean teeth. Or, they may have just been chewing it to soften it up before using it as an adhesive in toolmaking. Either way, scientists have recovered enough ancient DNA on one piece of 5700-year-old chewed tar to learn a lot about the human girl who chewed it. She had dark hair and skin but blue eyes, a combination that was common back then but is nearly extinct now. She also may have been a child based on the shape of the tooth marks.
Turpentine
Another byproduct of burning pine or birch in a kiln is turpentine, a solvent best known for its use in oil painting. It can also be obtained by slashing the bark of certain types of pine trees and collecting the oily sap, and then distilling it. Turpentine has long been used to make varnishes and thin paints, and used to be ingested as an attempted treatment for internal parasites before people realized how toxic it is to humans. It can also be refined further into camphor, a waxy aromatic substance that’s one of the active ingredients in VapoRub (along with turpentine as well–how old-fashioned), and rosin, used for increasing the friction of string instrument bows and as a flux core in solder that helps the molten metal flow.
Coke and charcoal
Coke is another substance that can be either made through burning coal in the absence of oxygen, or occur naturally. Coke is to coal as charcoal is to wood: their water and volatile components have been removed, resulting in fuels that burn hotter than their precursors, invisibly, and without smoke. This is important for food preparation in which smoky or sulfurous flavor is undesirable. Coke was an important fuel in regions with few trees, and in regions with lots of trees charcoal production caused massive deforestation in pre-modern times.
Interestingly, in the early development of steam locomotives, legislation was passed requiring them to run on coke so that they didn’t produce too much smoke. This meant that the earliest steam engines lacked the characteristic trailing plume of smoke. However, as railways scaled to industrial proportions, this rule was dropped to allow locomotives to use cheaper unprocessed coal. I wonder what the legislators were considering when they made that decision. Were they concerned about pollution? Or was it an aesthetic qualm? Coking, or producing coke from coal, requires the release of all that smoke anyway, but not where the locomotive is; it was common for the area surrounding coke furnaces to be completely denuded of vegetation due to the constant release of toxic fumes. Nowadays, there are systems to recapture these pollutants to reduce the environmental impact.
Coke is very important in both ancient blacksmithing and modern steel production. The high temperature at which it burns and the byproduct carbon monoxide allow it to smelt iron-containing ore into pig iron (so called because the shape of the mold it’s often cast into resembles a sow with a litter of piglets).
Activated charcoal is made by heating charcoal in the presence of steam, which causes it to puff up like popcorn and develop lots of microscopic internal pores. These allow it to adsorb substances (mechanically soak up, contrasing with absorption which requires dissolution or permeation of the absorbed material), making it useful in a lot of high tech applications such as air purification, medicine, sewage treatment, and others.
Creosote and naphtha
Creosote is a black gunky substance that often builds up inside chimneys and must be cleaned out by chimney sweeps. However, it’s not only a waste product–it’s a preservative, used to treat railroad ties and other outdoor wood components to prevent rot. It also used to be used in all kinds of medicinal treatments before people found it it causes cancer. The word “creosote” comes from the Greek for “meat preservative”, as the creosote present in smoke is responsible for the flavor and preservation of smoked meat.
Naphtha is a yellow oil historically used as lamp fuel and in warfare as Greek fire, a type of waterproof flamethrower made with naphtha and quicklime, which was used by the Byzantines to set enemy ships on fire. This ancient state secret helped the Byzantines win some important historical battles.
Nowadays, naphtha is commonly used to dilute heavy crude oil to make it easier to pump through pipelines, and is then recovered during processing and used again. It’s also the lighter fluid in wick-type cigarette lighters, which are rarer than non-wick types which use butane, and in certain camp stoves.
Potash
Potash (literally “pot” and “ash”) refers to a family of potassium salts, originally made by soaking wood ash in a pot with water and solvents and letting it evaporate. Potassium is named after potash, which makes me wonder whether it should be pronounced “pot-ass-ium” rather than “po-tass-ium”. The very first US patent ever granted, signed by George Washington, was for an improvement in the manufacture of potash. Potassium lye, a strong base, is a precursor to potash, and was historically used in making soap and bleaching fabric. (The more common type of lye today is sodium lye, which is used in making bagels.) Throughout its history of use, potash was consumed mainly as fertilizer. Today, it’s no longer produced from leaching wood ash, but is instead mined as potassium chloride and then processed into potash, but in the 1700s much of the wood cleared to prepare land for agriculture in the British colonies of America was used to make potash, which was exported to Britain.
One special type of potash is known as saltpeter or niter. Its most important use is in gunpowder, and it can be obtained in one of many ways. It can be easily harvested from guano, or made with more difficulty by burying human and animal excrement and watering it until the saltpeter leaches to the surface. There are lots of other ways to produce it nowadays using chemical reactions, but I won’t bore you with that.
In addition to its use in gunpowder, saltpeter has been used for preserving meat since antiquity. It’s still used in salami, bacon, ham, and frankfurters, which are classified by the WHO as Group 1 carcinogens, meaning there’s strong evidence that they cause cancer. This is the same tier that contains asbestos and cigarettes. Uh oh. However, as long as you don’t eat these processed meats every day the cumulative risk is low. The reason these meats cause cancer while other foods preserved with saltpeter, or even straight saltpeter pills (which were thought to be an anti-aphrodisiac, though there’s no evidence for it) don’t cause cancer is due to the way the saltpeter reacts with the myoglobin and hemoglobin present in red meat.
Another chemical that is a precursor to potash is cream of tartar, or half of the active ingredients in baking powder. The other half of baking powder is made up of baking soda, which is basic when dissolved in water, which reacts with the acidic cream of tartar to form carbon dioxide bubbles in a baked good to make it fluffy. Acid-base reactions are very fast: seventy percent of the bubbles are released when mixing, so when making something that’s leavened with baking powder, don’t overmix!
Cream of tartar is a byproduct of making white wine. It precipitates out when the wine is first cooled, forming a crystalline residue at the bottom of the bottle or the underside of the cork. This substance is collected and purified to use in cooking. This is an exception to the trend we’ve seen so far, that the old methods of production aren’t used anymore for most of these substances. In the case of cream of tartar, the most cost-effective way to make it is still straining it out of cooling wine or grape juice.
Cream of tartar is said to “stabilize” egg whites to allow them to be whipped better. It does this by lowering the pH of the eggs closer to its isoelectric point. This refers to the pH at which a molecule has no electrical charge, which is different for different types of molecules. When the proteins in eggs aren’t at the isolectric point, they all carry the same charge, which means that they repel each other. Taking away the charge of the proteins allows them to get closer together more often (“encourages protein-protein interactions” in technical parlance), and adhere to each other better.
Conclusion
Thanks for bearing with me through another non-paleontology-related post! I had a lot of fun learning about all these different materials and the way ancient humans figured out how to make and use them. The page image up top was generated by DALL-E 3, a new free online AI image generator, from the prompt “A group of cavemen using an underground kiln to make wood tar. They are pale skinned and are wearing clothing made of animal hides, and have protruding brow bones. The kiln is covered with rocks and earth and one caveman is stoking the fire. Style is risograph.” It was only a little over a year ago that its precursor, DALL-E Mini, generated this low-res wobbly art. That is absurdly fast progress!
Image Credits
Stoneware Alabaster Venetian Plaster Fresco La Brea Terva Leijona Greek Fire